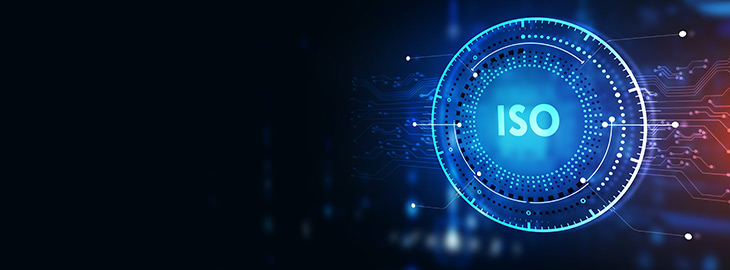
ISO 9000 and ISO 9001 are terms often used mixed when discussing quality management at an organization, but they refer to separate things. While both are related to quality assurance and ISO compliance and certification, they have distinct differences in their fundamentals and approach.
Understanding the difference between the two is crucial for any organization looking to implement a process approach to quality management and to follow the quality management principles outlined by the International Organization for Standardization, commonly known as ISO.
This article will cover the basics, benefits, and differences between ISO 9000 and ISO 9001 and address whether ISO 9001 is still relevant.
What Is ISO 9000?
ISO 9000 is an internationally recognized standard for quality management. It helps organizations to ensure that their products and services meet customer needs and regulatory requirements. Approved by the International Organization for Standardization (ISO), the standard provides a framework that helps organizations achieve customer satisfaction and continual improvement through a process-based approach.
ISO 9000 standards are not prescriptive. On the contrary, they are designed to be adaptable to different industries and organization types, promoting effective decision-making.
What Are the Benefits of ISO 9000 Compliance?
ISO 9000 compliance brings numerous benefits, including:
- Improved quality. ISO 9000 compliance helps organizations align their processes with international quality management standards to improve their products and services. The standard requires organizations to maintain a customer focus and to assess customer expectations regularly through internal audits, which can lead to fewer errors and customer complaints. Organizations can improve their quality management system and achieve sustained success by taking corrective action.
- Increased efficiency. ISO 9000 guides process management and continuous improvement, helping organizations to align their operations with international best practices. This can reduce waste and increase efficiency, leading to cost savings and improved profitability. Internal audits help organizations identify areas for improvement and ensure compliance with the standards, while certification by an accredited body can demonstrate an organization’s commitment to excellence.
- Enhanced reputation. ISO 9000 certification is recognized worldwide and can enhance an organization’s reputation in the eyes of consumers and stakeholders by demonstrating the organization’s commitment to quality and customer satisfaction. This can attract new customers, retain existing ones, and improve the organization’s standing in the marketplace.
- Better risk management. ISO 9000 compliance helps organizations identify and manage risks that may affect the quality of their products or services. By implementing a systematic approach to quality management, organizations can identify potential risks and take measures to mitigate those harms.
- Improved supplier relationships. ISO 9000 compliance can improve an organization’s supplier relationships by establishing precise quality requirements and expectations. By working with ISO-certified suppliers, organizations can ensure they receive high-quality products and services that meet their needs and expectations. This can help reduce supply chain disruptions and improve overall relationship management.
What Is ISO 9001?
ISO 9001 is a specific standard within the ISO 9000 family of standards. (ISO 9000 is a standard unto itself, and there are other standards in the 9000 family as well, beyond the scope of this article.) ISO 9001 outlines the requirements for a Quality Management System (QMS) that an organization must meet to be certified as ISO-compliant. These requirements include documentation, management commitment, process management, continuous improvement, and customer satisfaction.
The standard emphasizes meeting customer requirements and managing relationships with stakeholders. It also underlines the need for a process approach to quality management, which involves systematically identifying and managing business processes to ensure they meet the organization’s objectives.
Essentially, ISO 9001 is the internationally recognized standard for quality management systems. It is crucial for organizations that want to demonstrate their ability to provide products and services that fulfill regulatory requirements consistently.
Is ISO 9001 Obsolete?
No, it is not. ISO 9001 is one of the world’s most widely recognized and implemented standards. ISO standards are reviewed every five years and updated as necessary to ensure their continued relevance and effectiveness for organizations of any size or type.
The latest version of ISO 9001 was released in 2015 and is formally known as ISO 9001:2015. It introduced several improvements to the standard. These changes include a greater emphasis on risk-based thinking, increased focus on organizational context, and a more flexible approach towards documentation requirements.
For example, ISO 9001:2015 employs simplified language, a standard structure, and terminology that benefit organizations utilizing multiple management systems, such as those for health and safety, the environment, or business continuity. The updated standard provides better guidance for supply chain management and is more user-friendly for service and knowledge-based organizations.
ISO 9001:2015 is the current version of the standard, and it demonstrates an organization’s commitment to meeting customer and regulatory requirements, continuously improving its processes and products or services, and staying up-to-date with the latest industry best practices.
What Does It Mean to Be ISO Certified?
Being ISO 9001 certified means an organization has met the requirements of this specific international standard and has received certification from an accredited external certification body. ISO 9001 is the only standard in the ISO 9000 series focused on quality management systems.
To gain ISO 9001 certification, an organization must implement a quality system that meets the standard’s specific requirements. This involves establishing a quality policy, setting quality objectives, and improving processes to meet product quality goals.
ISO 9001 certification demonstrates to customers and stakeholders that the organization is committed to delivering quality. It shows that business owners have invested in following rigorous quality management principles and undergo regular audits by providers to ensure continued compliance.
Achieving ISO 9001 certification opens up new business opportunities and can provide organizations with a competitive advantage. It enables them to tap into new markets, meet supplier requirements, and boost customer retention by signaling their commitment to quality.
How to Become ISO Certified
While individuals cannot become ISO-certified, organizations can attain certification by following these key steps:
- Purchase the relevant ISO standard and thoroughly review the requirements. For quality management, this would be ISO 9001.
- Conduct a gap analysis to compare current practices against the ISO standard’s requirements. Identify areas that need improvement.
- Form a project team and appoint a management representative to spearhead the implementation.
- Provide training on meeting ISO standards across all levels of the organization.
- Create documentation like a quality manual, procedures, and work instructions to meet documentation requirements.
- Gradually implement the new quality management system aligned with ISO standards.
- Perform regular internal audits to uncover nonconformities that need correction.
- Work with an accredited external certification body to review processes and conduct an on-site audit.
- Make any necessary adjustments to comply fully with the standard.
- The registrar will issue an official ISO certificate if the organization satisfies all requirements.
- Maintain certification through ongoing audits and reviews. Re-certification occurs every few years.
The certification process usually takes 3-6 months, depending on the organization’s size and preparatory work done. With dedication and commitment, organizations can successfully achieve ISO compliance.
Best Practices for Successfully Completing Your ISO Certification
Gaining ISO certification takes careful preparation and diligent execution. Follow these best practices to ensure a smooth certification process:
- Secure total commitment from top management to implement the ISO 9001 QMS.
- Involve staff early to get input on QMS design based on the ISO 9000 family of standards, boosting engagement.
- Appoint a knowledgeable project manager to spearhead coordination and continual improvement.
- Develop a detailed project plan and timeline aligned to the organization’s size and complexity per ISO 9001 fundamentals.
- Provide comprehensive training on ISO 9001 requirements for all impacted staff focused on quality management principles.
- Perform internal audits to identify and resolve nonconformities before the formal ISO 9001 audit.
- Carefully select a reputable, accredited registrar to perform the ISO 9001 certification audit according to international standards.
Organizations can successfully achieve ISO certification with solid leadership commitment, employee involvement, and adherence to best practices. The result is improved operations, risk reduction, and a robust market edge.
RiskOptics for ISO Compliance
Employing reliable, high-quality Governance, Risk management, and Compliance (GRC) software is recommended to attain ISO compliance. The ZenGRC is a risk and compliance management solution that helps organizations identify areas where they comply with ISO standards and where gaps exist.
ZenGRC can guide organizations on how to fill those gaps to achieve compliance and keep them informed about the status of their compliance programs, leading to a faster, smoother, and more efficient path to ISO compliance.
Book a demo today to see how the ZenGRC can assist you in managing compliance.